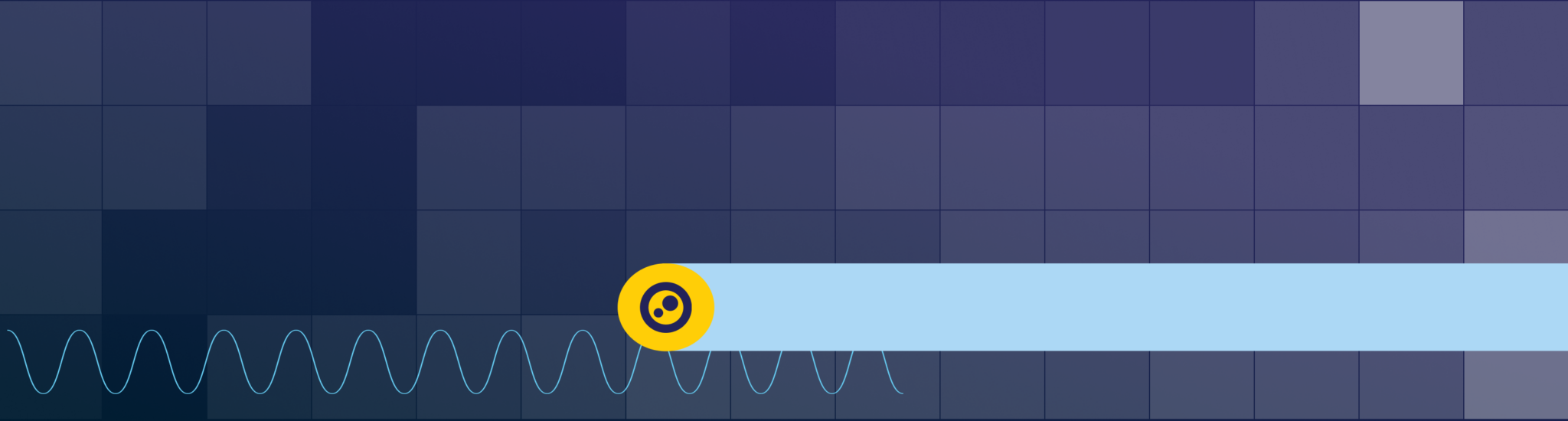
ATG Facilities
Overview
TRIUMF’s Radiochemistry Annex (RCA) facility, and its 30-person Applied Technology Group (ATG), support the cyclotron-based production of lifesaving diagnostic and treatment medical isotopes for the treatment of about 35,000 people worldwide every week. The facility is the core of TRIUMF’s industrial partnership with BWX Technologies, Inc. (BWXT) which owns three on-site cyclotrons operated and maintained by the ATG and housed in the RCA. The partnership makes Canada one of the world’s major suppliers of cyclotron-produced medical isotopes.
Medical isotopes are imaging molecules and therapeutic drugs whose active component is a short-lived radioactive isotope. These are the core of nuclear medicine, the field of health care that uses radiation for therapy and medical imaging.
A central challenge in the industrial-scale production of medical isotopes is that they have a fleetingly brief shelf-life. For example, iodine-123 (123I), used for cardiology, cancer and neurodegenerative condition imaging, has a half-life of just over 13 hours. Thus, 123I, as with the other medical isotopes produced, must be produced, extracted, packaged and shipped to hospitals in just hours.
With decades of experience and expertise in cyclotron operation and troubleshooting, the ATG delivers 24/7, 365 day, just-in-time medical isotope production with the knowledge that delays can mean life and death.
The TRIUMF-based facility is one of the world’s largest producers of strontium-82 (82Sr), used for high-resolution heart imaging to detect artery disease. Along with 123I, the facility also produces Indium-111 (111In) for targeted medical imaging, 68Ge generators for the production of 68Ga for general diagnostic purposes.
The use of U.S. Food and Drug Administration and Health Canada Good Manufacturing Practices in the RCA is enforced through routine on-site inspections from the two organizations and the Canadian Nuclear Safety Commission (CNSC).
This 40-year on-site industrial partnership began with Atomic Energy of Canada Limited (AECL), followed by Nordion, and today BWX Technologies. In 2004, TRIUMF and then-owner Nordion won the Natural Sciences and Engineering Research Council of Canada (NSERC) Synergy Award for Innovation for this longstanding university-industry partnership.
ATG's cyclotrons and facilities
HOW IT WORKS
RCA-based medical isotope production involves the close collaboration between TRIUMF’s ATG and on-site BWX Technologies staff.
The RCA’s main components for medical isotope production, all operated and maintained by TRIUMF engineers and technicians, are: three cyclotrons and a control room; hot cells for target handling; beamlines; rabbit lines for target transportation; and the overall building services.
The RCA’s cyclotrons are a CP 42 (now discontinued due to its age) and two TR 30 cyclotrons, the latter two manufactured by Richmond B.C.-based Advanced Cyclotron Systems Inc. TRIUMF and EBCO collaborated on the design and manufacture of the original cyclotron , hence the name TR-series. These medical cyclotrons are high intensity compact commercial cyclotrons. The prototype was TRIUMF’s TR 13 cyclotron. More recently, TRIUMF’s new IAMI facility will house a new TR 24 cyclotron.
The medical isotope production targets are manufactured by ATG and plated by BWX Technologies radiochemists. They are then transferred to TRIUMF staff who handle all aspects of cyclotron-based irradiation, returning the transformed target to BWX Technologies staff. The TR-30s operate with both gas and solid targets.
The solid targets are transferred between BWX Technologies and TRIUMF staff using a pneumatic transfer system between the cyclotrons and a hot cell. The pneumatic transfer system consists of a rabbit, a container that carries the target within it and named for its quick, rabbit-like speed, that travels inside a radiation-shielded pipe.
Each hot cell is surrounded on all sides by 6” radiation-shielding lead bricks and a lead-shielded door with a thick leaded glass window that provides a view of the interior. Technicians use a robotic arm to access and manipulate objects in the hot cell’s interior.